Thermal imaging uses infrared cameras to spot overheating wires safely and quickly. By capturing heat patterns, you can identify hotspots caused by loose connections, overloads, or damaged insulation before they turn dangerous. It’s a non-contact, efficient way to monitor electrical systems in real-time. With thermal images, you’ll easily spot problems early, reducing safety risks and repair costs. Keep exploring to learn how to conduct these inspections effectively and interpret the results accurately.
Key Takeaways
- Thermal imaging quickly identifies hotspots in wires, indicating potential overheating or overloads.
- Infrared cameras provide a safe, contactless method for inspecting energized electrical systems.
- Analyzing thermograms helps detect loose connections, damaged insulation, or overloaded circuits early.
- Proper calibration and multiple angle scans improve accuracy in pinpointing overheating points.
- Thermal imaging supports preventative maintenance, reducing fire risks and equipment failures.
Understanding the Risks of Overheated Wires
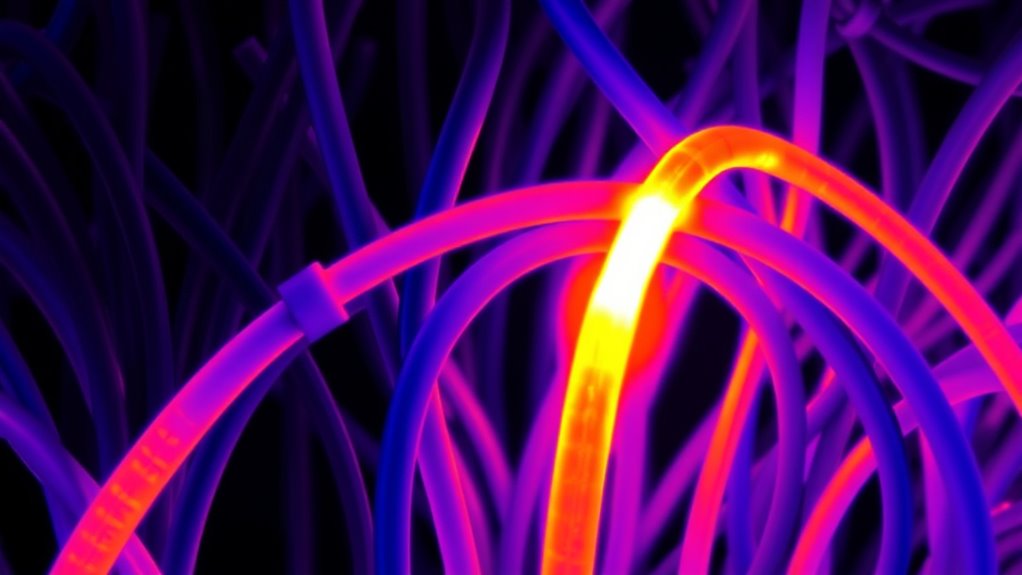
Overheated wires pose serious safety risks that can lead to electrical fires and equipment damage. When wires heat beyond their safe limits, the insulation can melt or degrade, increasing the chance of short circuits. This overheating often results from overloaded circuits, loose connections, or damaged wiring. Ignoring these signs can cause sparks, fires, or even electrical shock hazards. Over time, persistent overheating weakens the wire’s integrity, making future failures more likely. You might not notice the problem until it’s severe, which is why early detection is critical. Recognizing the dangers of overheated wires helps you take proactive steps to prevent accidents, protect your property, and ensure safety for everyone around you. Additionally, understanding the contrast ratio of your wiring system can help identify potential issues related to power distribution and thermal management.
How Thermal Imaging Works in Electrical Inspections
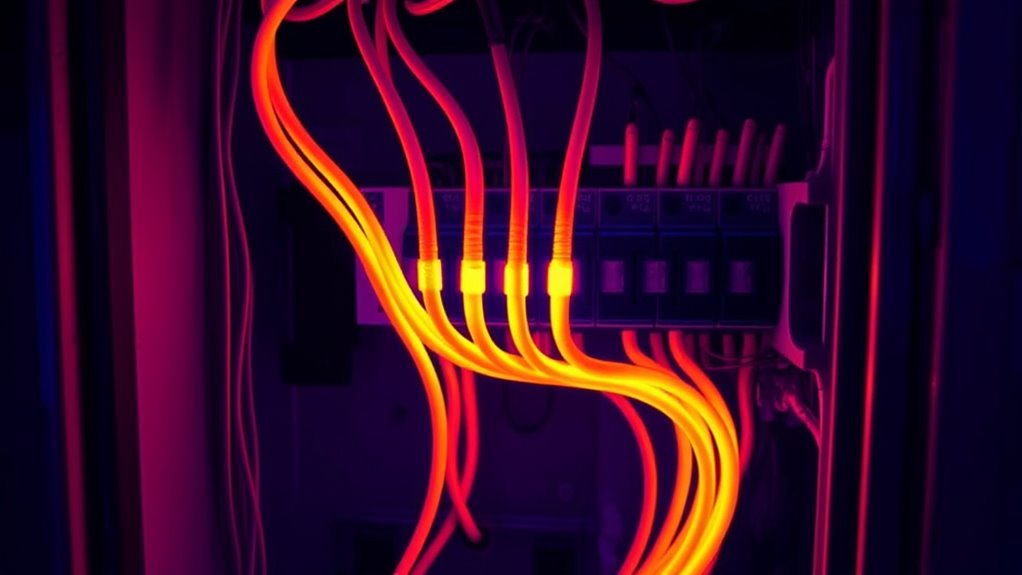
Thermal imaging has become an essential tool in electrical inspections because it allows you to detect hotspots that indicate potential problems. The process uses infrared cameras to capture the heat emitted by electrical components. These cameras detect variations in temperature, creating detailed thermal images or thermograms. When you scan an electrical system, the camera translates heat differences into visible colors, highlighting areas that are unusually hot. Hotspots appear as bright or dark spots, depending on the camera’s color palette. This real-time visualization helps you quickly identify overheating wires, loose connections, or overloaded circuits before they cause failures or fires. Because thermal imaging is contactless and non-invasive, you can inspect energized systems safely and efficiently, gaining critical insights without disrupting operations. Recognizing common tuning modifications in vehicles can also help you better understand how electrical systems might be affected by performance upgrades.
Advantages of Using Infrared Cameras for Hotspot Detection
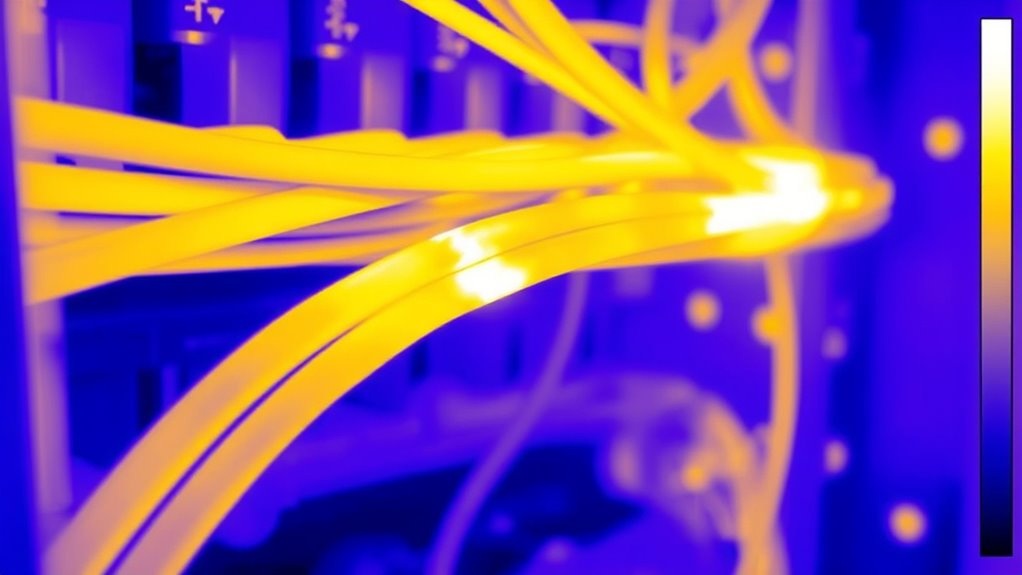
Using infrared cameras for hotspot detection offers several key advantages that make them invaluable in electrical inspections. They enable you to identify overheating components quickly without physical contact, reducing safety risks. Infrared cameras provide real-time thermal images, allowing you to pinpoint problem areas instantly. They also detect issues before failures occur, saving you time and money on repairs. Additionally, infrared cameras are non-invasive, so you can inspect live systems safely. Their high sensitivity and accuracy make them reliable tools for maintenance. Here’s a quick comparison:
Feature | Benefit |
---|---|
Non-contact inspection | Ensures safety and convenience |
Real-time thermal imaging | Immediate detection of hotspots |
Preventative maintenance | Spot issues early to avoid failures |
User-friendly interface | Easy to operate, even for beginners |
Cost-effective | Reduces downtime and repair costs |
Being aware of the lifestyle benefits of remote work can also improve your approach to maintenance routines, allowing for more flexible and efficient inspections.
Steps for Conducting a Thermal Inspection of Electrical Systems
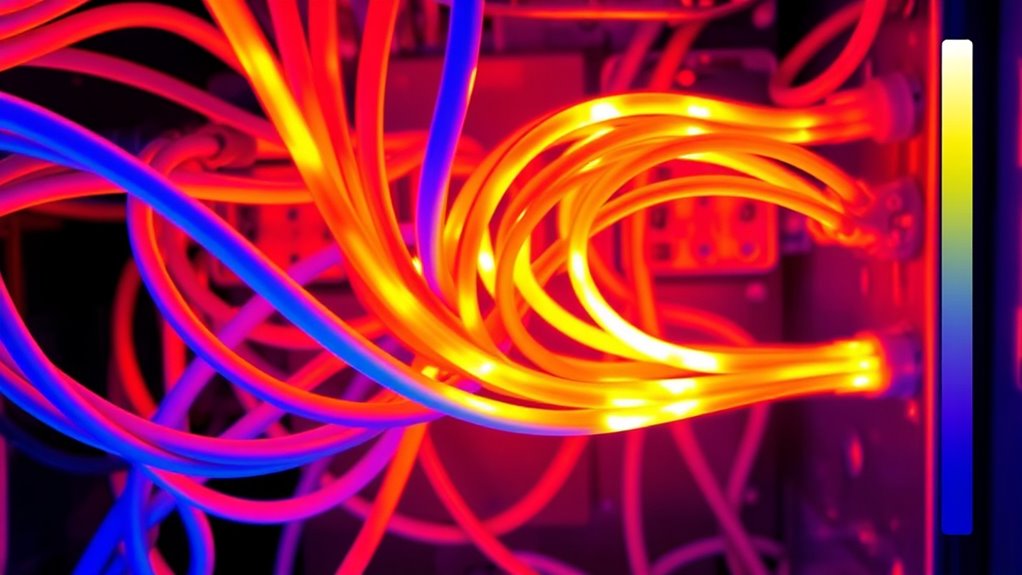
To guarantee a thorough electrical system inspection, you should follow a systematic approach that involves preparation, scanning, and analysis. Begin by reviewing electrical schematics and identifying critical components or known problem areas. Ensure your infrared camera is calibrated and set to the correct parameters for the environment. Before scanning, turn off unnecessary loads and eliminate sources of interference. Move the camera slowly along the electrical panels, wires, and connections, capturing thermal images from multiple angles. Be thorough, covering all accessible components. After completing the scan, review the images carefully, noting any hotspots or abnormal temperature variations. Proper documentation is essential. Regularly updating your knowledge about safety protocols and best practices can significantly enhance the accuracy and safety of your inspections. This methodical process helps you detect potential issues early, minimizing risks and preventing costly failures.
Interpreting Thermal Images to Identify Potential Problems
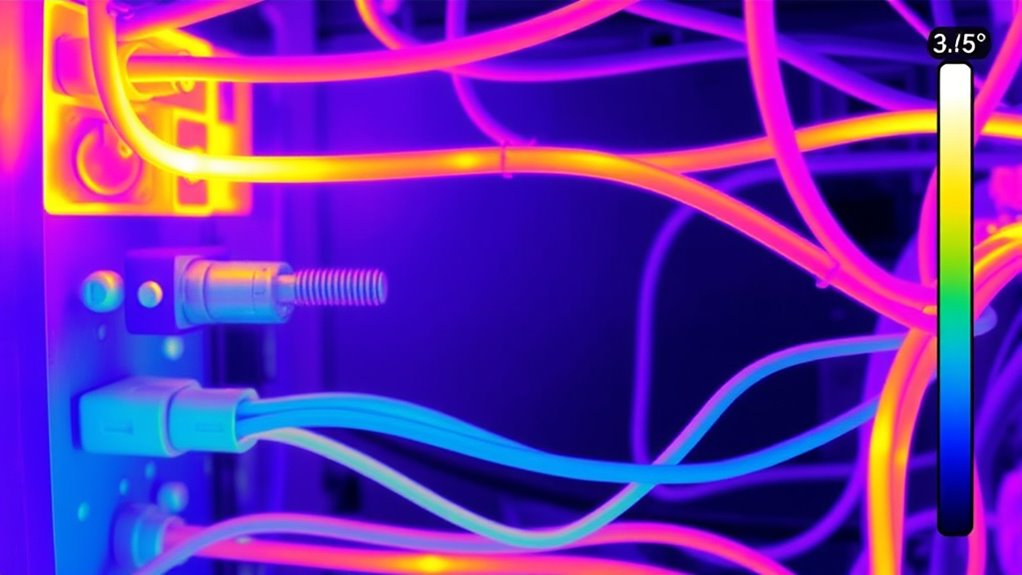
Interpreting thermal images accurately is essential for identifying potential electrical problems. You need to look for hotspots—areas notably warmer than surrounding components—that may indicate overheating. Consistent high temperatures in specific wires or connections suggest a problem, while uneven heat distribution can point to loose or corroded contacts. Keep in mind that some components naturally run hotter; focus on abnormal temperature rises rather than normal operation. Use color scales to compare areas and identify deviations. Always consider ambient temperature and equipment specifications to avoid false alarms. If you spot a hotspot, plan a follow-up inspection or repair. Proper interpretation helps prevent failures, fires, and damage, ensuring electrical systems operate safely and efficiently. Additionally, understanding best practices for thermal imaging can improve detection accuracy and safety during inspections.
Frequently Asked Questions
What Is the Typical Cost of Thermal Imaging Equipment for Electrical Inspections?
You’re wondering about the typical cost of thermal imaging equipment for electrical inspections. Generally, these devices range from $2,000 to $10,000, depending on features and resolution. Entry-level models are more affordable but offer fewer capabilities, while professional-grade cameras provide detailed thermal analysis. Keep in mind, investing in quality equipment guarantees accurate detection of overheating wires, which can prevent costly electrical failures and improve safety.
How Often Should Thermal Inspections Be Performed on Electrical Systems?
A stitch in time saves nine, they say, and that applies here. You should perform thermal inspections on your electrical systems at least once a year, or more frequently if you notice signs of wear or increased load. Regular checks help catch issues early before they turn into costly failures or hazards. Staying proactive guarantees your system stays safe and efficient, saving you time and money in the long run.
Are There Safety Precautions When Using Infrared Cameras on Live Wires?
When using infrared cameras on live wires, safety is vital. You should always wear proper personal protective equipment, like insulated gloves and safety glasses. Keep a safe distance from energized components and avoid direct contact. Use the camera’s features correctly, and make sure you’re trained in its operation. Always follow electrical safety protocols and manufacturer’s instructions to prevent shocks or accidents while inspecting live electrical systems.
Can Thermal Imaging Detect Issues in Underground or Hidden Wiring?
You wonder if thermal imaging can spot problems in underground or hidden wiring. While thermal cameras excel at detecting surface heat variations, they struggle with buried or concealed wires since heat dissipates into surrounding materials. You need to look for other methods like ground-penetrating radar or specialized sensors to identify issues in hidden wiring. Relying solely on thermal imaging might leave you blind to some underground problems.
How Accurate Are Thermal Cameras in Predicting Electrical Failures?
You want to know how accurate thermal cameras are in predicting electrical failures. These cameras are quite effective because they detect temperature differences that indicate potential issues before they cause failures. However, their accuracy depends on proper calibration, environmental conditions, and the technician’s skill. While they provide valuable early warnings, you shouldn’t rely solely on them; combining thermal imaging with regular inspections guarantees better predictive maintenance.
Conclusion
By using thermal imaging, you can quickly identify overheating wires before they cause a fire. For example, in a recent commercial building inspection, infrared cameras revealed a hotspot in a circuit panel, preventing a potential electrical failure. Regular thermal inspections empower you to catch problems early, saving money and ensuring safety. Embrace this technology to protect your property and stay ahead of electrical issues before they escalate.